In early 2022, transportation and logistics officials at Tyson Foods Inc. began developing a plan to address multiple issues in its supply chain by removing drivers from some of its refrigerated delivery trucks. This past September, the company made good on that commitment by starting a pilot program that will deploy four trucks in Northwest Arkansas to eliminate the need for drivers for short, shuttle routes to deliver products from processing plants to its cold storage facilities and distribution centers. The initiative is based on a partnership with Gatik AI Inc., a Silicon Valley company specializing in autonomous shipping of goods between distribution and fulfillment centers and their retail partners to streamline this specific part of the commercial supply chain.
The initiative is being led by Patrick Simmons, vice president of transportation, who joined Tyson about two years ago after working for the previous 22 years in similar supply-chain roles with Walmart and Sam’s Club, including warehousing, transportation and logistics. Prior to that, he learned about automation and drone technology while serving in the military for about 10 years on active duty.
“We are innovating using automation and technology throughout all of Tyson as part of a broader companywide digital enablement strategy,” Simmons said. “We’re trying to take advantage of new technology that’s out there so, this piece of technology is an autonomous truck or self-driving truck. We believe it will strategically enable us to place our private fleet drivers where they are needed most — which I would define as customer-facing deliveries — while allowing us to still operate reliably and safely transport products from our plants to our distribution centers.”
Team approach
The partnership with Gatik made sense for Tyson, as the company’s track record includes filling a similar role for Walmart since late 2020 and more recently with Kroger. Having spent the past two-plus decades working in transportation and logistics in Northwest Arkansas, Simmons was aware of the company’s expertise and good reputation, including its successful collaboration with retail giant Walmart.
“I would say they own the middle mile of autonomous trucking capabilities,” Simmons said, echoing Gatik’s slogan. “They are the industry leader in this space and their safety record is impeccable.”
He explained the goal of this middle mile solution is to close the gap between Tyson facilities. The Gatik trucks are not going to a storefront or to one of Tyson’s large customer’s distribution centers. The shipments are going to another Tyson internal location.
“We’ve identified about 40 different locations across the United States where we could do this in the future,” he said.
Soon after the early September announcement about Tyson’s plan to deploy four, customized 26-foot refrigerated trucks from Gatik, equipped with AI-enhanced autonomous technology, the company deployed its first truck days later. During the testing phase, the trucks are manned by a back-up/assistant driver as a precaution.

“They’re not a 53-foot tractor trailer but a 26-foot straight truck type of refrigerated delivery vehicle, designed to our specifications. What it is going to do, for example, is allow us to take products from a production plant to another Tyson facility where it would be breaded,” Simmons said. “If you think of Wendy’s chicken patties that get breaded; it’s done at another plant other than the production facility. They also transport to off-site cold storage facilities.”
Until the pilot is complete and more autonomous vehicles are deployed, “We have a 53-foot tractor trailer with a Tyson driver that does shuttle loads back and forth between essentially Rogers, Ark., and Springdale, so about 10 miles each direction,” Simmons said. “That is not the type of work that most of our truck drivers like to do. It’s heading out into traffic; it’s not getting on the highway and getting the truck up to 65 miles an hour and driving 300 or 400 miles, which is about our average length of a typical haul. The driverless truck will do the busy work,” with the shorter, shuttle routes from one part of Tyson’s internal business to another.
“That will free up our driver that uses the 53-foot tractor trailer to go do other things. By not being tethered to the short, shuttle routes around Northwest Arkansas, the drivers of the bigger rigs making longer hauls are able to do what they do best and what most of them prefer,” Simmons said.
Considering that one Tyson driver during a 52-week year will typically drive just over 700 loads a year, the savings that can be realized by automating the shuttle trips add up, according to the company.
“What that equates to for us is value of about $480,000 for what that repurposed driver is now able to do,” said Simmons.
Gautam Narang, Gatik’s chief executive officer and co-founder said the opportunity to provide Tyson with the ability to transport refrigerated and frozen foods quickly and safely using trucks with multiple sensor modalities ensures the company’s fail-safe success in its short-haul B2B operations from processing facilities to cold storage and distribution centers.
“We’re excited to partner with Tyson Foods to reduce cost and complexity within their regional distribution architecture,” Narang said when the partnership was announced. “This is a significant moment for Gatik as we introduce Class 7 autonomous box trucks into our fleet. Our partnership with Tyson is poised to drive long-term innovation and supply chain resiliency while delivering tangible, near-term value.”
Simmons said the remaining three autonomous trucks that are part of the pilot plan are expected to hit the road soon, with two more expected to come online in late October or early November and the fourth to be added in early 2024. Not unlike the food industry, supply chain challenges slightly delayed the delivery of the remaining three vehicles, he said.
“Their supply chain has struggled with some of the technology parts and pieces coming in because it’s a specially design truck just for our type of business,” Simmons said.
As the company continues growing, expanding and acquiring additional operations, not every place where Tyson produces its various products has enough storage capacity in terms of refrigerated or freezer space, so it uses a lot of storage space in Northwest Arkansas while utilizing distribution centers in the area to store and stage orders for shipment.
“We chose this area [to start the pilot program] obviously because we’re close to it and can study it,” Simmons said.
The plan is to operate the autonomous trucks 18 hours a day even though, theoretically they could be driving 24 hours a day. That’s a significant contrast to traditional fleet drivers or third-party contractor drivers that are only allowed to drive 11 hours per day for safety reasons. Besides those limitations, there are also expenses related to human drivers that aren’t incurred with autonomous technology, including training, scheduling limitations and paying drivers’ salaries and benefits. First and foremost, the shortage of truck drivers is real and will likely only get worse.
“Drivers are in short supply. They were prior to COVID and that shortage was highlighted during COVID and post COVID there is still going to be a shortage.
“Because that truck is operating 18 hours a day, it’s actually operating more efficiently than a 53-foot truck and trailer that operates 11 hours a day. And if we wanted to operate 18 hours a day with a live driver and a 53-foot tractor trailer, we’d have to have two drivers, two sets of everything to get things done.”
Simmons clarified: “We’re not trying to get drivers out of the equation at all. There aren’t enough drivers going forward so this allows us to repurpose some of our drivers and augment our workforce with an autonomous truck.”
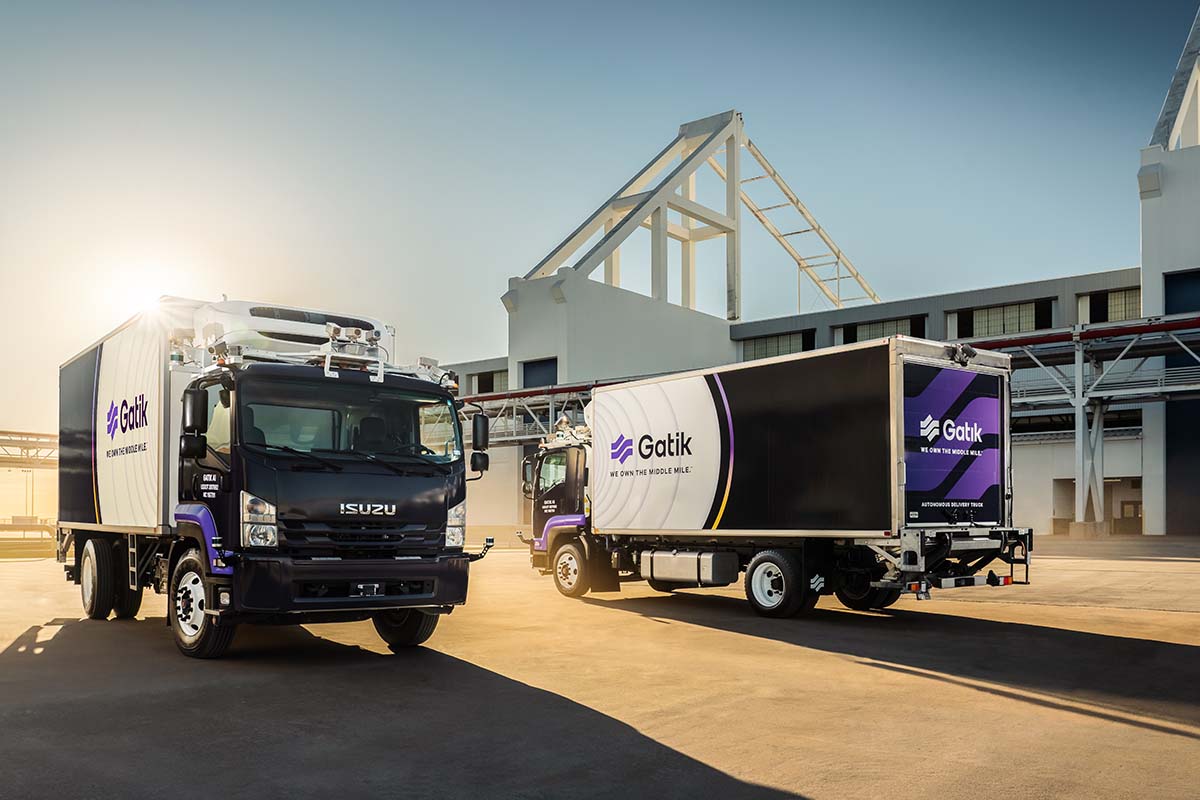
Safety counts
He said as the pilot progresses the amount of time an assistant driver is in the cab varies with each truck, based on safety data collected by Gatik. The company also sets specific, predetermined safety triggers for each pilot program. During the pilot, the assistant driver sits in the driver seat like any other vehicle. Eventually they move into the passenger seat and eventually they move out of the truck.
“Once it hits all their safety checks then that truck will become fully autonomous,” Simmons said.
He added that Tyson’s initial pilot has not yet reached those triggers.
“I think on average that takes anywhere from four to six months before they let it operate totally autonomously.”
Gatik boasts a sterling safety record since its founding in 2017. It has autonomous trucks deployed in Texas, Arkansas and Ontario and to date, it doesn’t have any reported accidents or incidents among its autonomous trucks, an enviable achievement among any traditional, human-driven commercial fleet.
“I wish our private fleet could operate as safely,” Simmons said, “and we have one of the safest private fleets on the road. But we still suffer from human error.”
To address anomalies during a shipment, Gatik maintains monitoring stations where every vehicle’s progress is watched on video screens that transmit footage from each truck, which is equipped with cameras, sensors and radar technology providing 360-degree views around. However, if something abnormal happens, the person monitoring the truck can intervene.
“It’s pretty impressive what it can do,” Simmons said.
Looking ahead, Simmons said future phases of the autonomous truck program will prioritize minimizing the environmental impact of the diesel-fueled driverless fleet.
“No one has asked Gatik to provide battery-operated equipment before so I would say kind of our next phase after this is we want to have an electric truck that runs on batteries, so they’re working on designing that for us,” he said. “That would help us reduce carbon emissions in the future.”
While payloads and mileage between charges could be compromised by the size and weight of a giant battery needed for that truck, Simmons said Tyson isn’t looking at a solution for long hauls.
“We’re not going 400 miles a day; we’re going 10 miles at a time, and we think it’d be a good fit for us,” he said. “And we think we could dramatically reduce our carbon footprint in the future.”