Does trying to find out what happened after a major downtime or quality issue make you feel like you are taking part in one of Abbott and Costello’s “Who’s on first” routines? Often, the reason for confusion stems from finger pointing between maintenance and production departments, neither claiming accountability when something bad occurs, but both anxious to take credit for any positive developments.
When there is downtime, maintenance takes the heat and when production records are set – production gets the credit. It is a no-win situation for the maintenance manager to tell management, “We had an awesome day. We had zero downtime.” After all, it is the maintenance department’s job to ensure there is zero mechanical downtime. So, how can a maintenance department elevate itself to being just as important in success as it is in failure? By building a partnership with the production department that shares in ‘traditional’ production or QA roles.
For example, in a poultry plant’s first-processing department, whose responsibility is it to make adjustments to first-processing equipment like the venter, the vent opener and the eviscerator? Historically, those adjustments are made by maintenance mechanics. But who initiates those adjustments? Often, QA will discover an issue while performing a QA check or a production worker will call for maintenance to make an adjustment. In this kind of working relationship, there are two issues: 1) Maintenance will either agree that an adjustment needs to be made or not, setting up an adversarial relationship; 2) The changes are conducted verbally and no one ever documents what was done to “fix” an issue, setting up the opportunity for a “he said/she said” discussion later.
Conduct clearly defined checks
Why not just let maintenance mechanics conduct clearly defined checks on the equipment for which they are responsible and document those checks? In SPC terminology, this might be referred to as setting up a control chart, though it does not have to be nearly as technical. Your facility likely already has some of these checks being conducted by QA. When they find a condition that is out of range, they “tell maintenance” and that usually ends the discussion until the next check. But, what if a maintenance mechanic does his own check, makes his own adjustment and documents that adjustment using what’s called a “process monitor”? This would leave QA or production to simply verify that production is in control.
Often, there is a great hesitancy for maintenance departments to take on this kind of documentation (aka, accountability). It is understandable given the culture of most maintenance departments is that of being EMTs who get called into action after receiving their 9-1-1 calls on their radios. This mentality relieves them of the responsibility of taking the “blood pressure” or “pulse” of the patient until after they receive the call for help. But, would a better analogy be the one of the nurse whose duty it is to monitor the patient throughout their shift, consistently taking their blood pressure and pulse, and making small adjustments to the patient’s treatment before there is a need to call a doctor? This is quite a shift in mindset and requires a little time for it to take hold.
And, of course, there is the additional responsibility of actually initialing a document that says, in effect, “I have made these checks and I verify they are accurate.” This is quite a change from responding to a conversation where a production supervisor or QA tech says, “This equipment needs adjustment.” It means the maintenance department is accountable to be proactively working for the benefit of the production and QA department. This makes maintenance just as responsible for the success of production as it is responsible for the failure when there are mechanical issues.
More advanced maintenance departments record the data from these process monitors directly into databases via stationary workstations in the department, notebooks or more recently, WiFi enabled tablets. Having this data in electronic form means you can easily manipulate the data to view all kinds of various attributes and trends. This type of ability is becoming much more affordable and increasingly necessary to address issues in your operations. When you can combine this data with production-related data involving attributes like bird weights and breeds, you can begin to see patterns emerge and will be able to better dial in equipment to improve yields.
These guidelines will hopefully eliminate any future Abbott & Costello-like routines. When there is an issue, either side can pull out their process monitor and have a roadmap of exactly what occurred throughout the shift and how they responded to it.
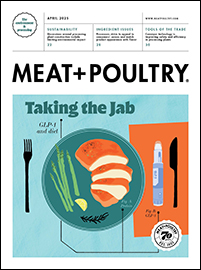