The most enjoyable part of my job is visiting packing and processing plants, witnessing first-hand the expert hand-craftsmanship (such as at Allen Brothers’ Chicago plant, which is featured in this issue) and various in-plant technologies, but most importantly meeting the people who make these facilities hum.
While reflecting on the plants visited this year, one plant clearly stands out — Hormel Foods’ Austin, Minn., plant. (See the June 2012 cover story in Meat&Poultry.)
This 1.1 million-sq.-ft. facility turned 30 years old in September. What’s scary is I remember visiting the construction site of this plant on a cold winter’s afternoon in the early 80s and stumbling over frozen mud and foundation work while taking notes.
The original Austin plant spanned 54 acres, towered nine-floors high at the tallest spot and was the largest meat plant in the world in its heyday. The facility today remains one of the largest meat plants in the world – and is a modern technological marvel.
This plant is six plants under one roof – dry sausage, meat products, grocery products (canning), shipping warehouse, harvest and fabrication plus a large refinery operation – all connected by common passageways. It employs almost 1,750 people.
Products manufactured total 1.3 million lbs. per year, representing about one-eighth of the annual product volume produced by the entire company.
The Austin plant is different in many ways. Hormel has a partnership with Quality Pork Processors Inc., which is located at one side of the facility. All fresh pork QPP processes goes to Hormel Foods, which utilizes the meat cuts and trimmings throughout the Austin facility.
The facility’s Automatic Storage and Retrieval System (ASRS), which has been operating since day one, is a 14-level-high, computerized warehouse that stores and retrieves products by bar code.
Hormel’s high-pressure processing system used on some of its products was initiated in the Austin plant through R&D. Many ergonomically designed pieces of machinery and assists eliminate physical stresses created by some jobs on the line.
As this plant evolves, space keeps getting tighter, but Hormel manages to squeeze more production out of it each year through innovation, not by adding brick and mortar.
But more than anything else, Hormel executives credited their employees for making the company successful. Most workers I spoke with credited teamwork and working closely together for the facility’s continued success.
During my long drive home, it dawned on me the one thing all successful companies I’ve visited over the years have in common are caring, hard-working employees.
Here’s a big “thank you” to the thousands of men and women who work tirelessly every day behind the scenes at meat and poultry facilities all around the country.
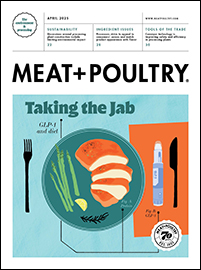